Table of Content
New Jersey has the highest land value in the country—over $196,000 per acre. Modular construction is relatively eco-friendly to begin with, but Deltec Homes takes it a step further. Because the company uses proprietary building practices such as super-insulated walls and trusses, a Deltec home is potentially three to five times more airtight than typical buildings. And, by focusing on natural comfort from solar heating and passive cooling, Deltec Homes has been recognized for innovation by the U.S.
We’ve had the best home purchase experience at Oak Creek Homes thanks to Millie. She’s gone above and beyond making sure my mom has everything she needs in a new home and the easiest process possible. Also, home buyers will want to understand that all of the appliances and mechanical systems in the home will carry their own warranties.
Building Modular near Lake Placid 🏡🌲
Folks who’d rather go a different route than a basic Cape Cod or ranch-style modular will want to consider Connect Homes. As one of the top modern modular home manufacturers, Connect offers truly modern designs that are clean, sleek, and efficient, making its models attractive to folks whose tastes don’t fit in a box. Pricing ranges between $332 to $543 per square foot and includes design, installation, tax, and site work. Home buyers looking to balance options, price, and speed might consider going with Clayton Homes. This modular home builder offers a wide range of modular homes, some of which start at around $60 per square foot before customizations. Clayton services the entire nation and is the recipient of multiple 2022 Manufactured Home Institute Excellence in Manufactured Housing Awards.

Also, modular homes tend to be larger and consist of beefier framing members. Connect Homes provides a streamlined collection of home floor plans, with 15 models available. While no two models are wildly different, sizes and shapes may vary to meet home buyers’ tastes. However, it can be difficult to compare these models side by side thanks to the company’s challenging web design.
Custom Modular Home Design.
Luckily, the timeline for Connect Homes is about 5 to 7 months from the beginning of construction to installation, so time spent struggling on the website won’t be in vain. But Impresa Modular is good for more than just custom builds; the brand has hundreds of available floor plans that customers can choose from. Aside from the mandated 1-year warranty, there is no warranty information listed on the site. But the 3- to 4-month lead time from construction to installation is very fast—especially for a custom build.

To find the best-manufactured homes we sorted through more than a dozen manufacturer websites, including subsidiaries of larger conglomerate manufacturers—like Champion Home Builders, Cavco, and Clayton. We assessed the availability and floor plans using geographic locations in the Eastern, Southern, and Western regions of the United States to compare the variety of homes available. Shopping for a manufactured home doesn’t mean that you have to compromise in terms of energy efficiency. Instead, seek out a mobile home manufacturer committed to quality construction, keeps drafts to a minimum, and contributes to a tight building schedule and lowerenergy costs. When shopping for a manufactured home, the research should begin with comparing the best mobile home manufacturers. Since this type of home is built start-to-finish inside the manufacturer’s facility, you want to be sure that the materials and workmanship meet your standards and expectations.
Why manufactured homes?
For a heavy-built house that will stand up to years of use, check out the modular homes available from Deer Valley. This mobile home manufacturer produces a variety of impressive modular home floor plans that will be a great match for a home site with a permanent foundation. New Jersey Modulars has a unique relationship with fellow modular builder, Beracah Homes. We proudly build our homes using their innovative factory-build process that features precision engineering, strict environmental control, and faster build times. Thanks to this unique building process, we are able to offer a wide variety of styles, designs and floor plans. You can customize – mix and match plans, change rooms, layouts – and we’ll work with you to create the home of your dreams.
Part of the Cavco family of brands, Fleetwood offers spacious mobile homes that accommodate families. A lineup of double-wide manufactured homes with up to five bedrooms composed of 1,800 or more square feet of living space will be spacious enough for most families. Depending on the region you’re shopping in, series like the Canyon Lake, Westfield Classic, or Sandalwood XL might be good options to consider. Also, beyond changing floor plans, almost all modular home manufacturers offer custom finish options.
This custom modular home manufacturer allows shoppers to design their homes from scratch using the company’s interactive design tool, HomeStyler. Impresa’s collaborative custom-design process ensures the customer is getting exactly what they want, and prices range between $200 and $245 per square foot. With access to interior walls throughout the building process, typical air infiltration points are sealed better than with onsite construction. What this means to you is that the building envelope of your custom home is fabricated to be super energy efficient. Increased insulation, high-tech sealants, and the use of advanced materials are just some of the reasons to decide on the advantages of modular building for your custom home.
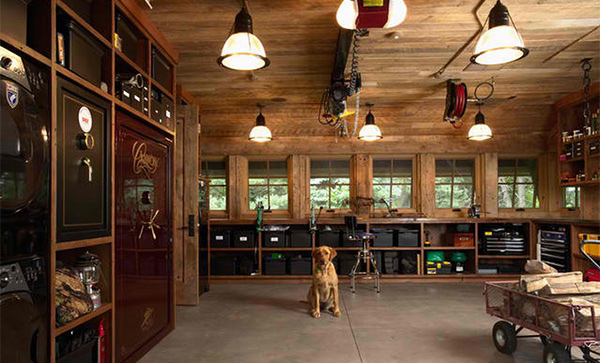
These are often the most affordable mobile homes to buy but may have limited layout options. Multi-section manufactured homes are greater than 20 feet in width, with the individual sections assembled on-site. Another type of manufactured home to consider is a modular home, which is factory-built similar to a manufactured home but is finished on-site and must meet local building code requirements. If you’re shopping specifically for manufactured mobile homes, there are plenty of floor plan options. Depending on your location, Champion offers two dozen or more single-section mobile home plans and nearly double that in multi-section homes. Choosing the right builder to provide your new home is one of the most important decisions you will make in the home buying process.
Home buyers will want to leave room in the budget to account for these potentially hidden costs. Eighty to 90 percent of a modular home is completed in the factory, leaving 10 to 20 percent left for the site crew. Once the sections of the home are installed and married together, the homeowner can choose to finish the work themselves . Many folks opt to have the bottom floor finished by the crew and leave the upstairs unfinished, allowing them to save some money with sweat equity. One of the biggest benefits of going with a Clayton home is the time to completion.
Factory-built homes can also leverage the buying power of large quantities of quality construction materials, resulting in greater savings on your new home when compared to the cost of a stick-built home. Assembly line construction means frequent inspections and opportunity for good oversight of workmanship at every stage. On a technical note, manufactured homes sit on a permanent steel chassis while modular houses are removed from chassis used for transport and instead rest on a permanent foundation. In both cases, these homes are considered factory-built and some manufacturers produce both mobile and modular homes.
Commodore Homes is one of the more budget-friendly options, allowing home buyers to manage their budget carefully. Commodore ensures the home buyer will know exactly what they’re getting into by providing a comprehensive budget calculator tool. This tool considers every factor, from site work to electrical hook-up, to help buyers know exactly what they can spend on a modular home. Site preparation is the responsibility of the property owner, not the manufacturer. This means that any excavation, septic, well drilling, electrical service, and foundation work need to be performed before the modular home is delivered. In many cases, the homeowner will hire a general contractor to handle these tasks.
Get answers to our most frequently asked questions about modular homes. Family owned and operated since 1959, Jacobsen Homes has a reputation in Florida as the number one source for manufactured Homes, mobile homes, andmodular homes. Click here to find a retail center or community within your desired area of Florida. The biggest modular home manufacturers generally have a handle on any shortages, ordering large quantities of materials ahead of time.
Deltec Homes
Depending on the area in which a home buyer lives, there may be many manufacturers to choose from. For this reason, it becomes extremely important that they do their research on modular homes and the process. By building in controlled environments, Affinity Building Systems can construct in a much more efficient manner, while not at the mercy of weather and other delays. Our manufacturing facility is housed over 2 ½ acres and is contained on our private 13-acre complex. We pride ourselves in treating our workers and builders with care and respect; which we believe, in return, promotes quality-building practices. Most of our plans can be engineered to meet building code requirements up to and including 180+ mph wind zones.
No comments:
Post a Comment